How Lean Logistics Practices Can Help Businesses Achieve Efficiency and Cost Savings
Introduction:
Logistics is a critical aspect of business operations. It involves the management of the flow of goods and services from the point of origin to the point of consumption. Lean logistics practices have become increasingly popular among businesses looking to improve their operations. Lean logistics involves the implementation of lean principles in logistics operations to eliminate waste and increase efficiency. This article will explore the benefits of lean logistics practices for businesses.
Increased Efficiency:
One of the primary benefits of lean logistics practices is increased efficiency. By eliminating waste and streamlining processes, businesses can improve their overall efficiency. This leads to a reduction in lead times, improved delivery times, and better customer service. For example, by using just-in-time delivery methods, businesses can reduce inventory levels and eliminate the need for costly warehousing.
Reduced Costs:
Another benefit of lean logistics practices is reduced costs. By eliminating waste, businesses can reduce the cost of materials, labor, and transportation. This leads to lower overall costs and improved profitability. For example, by implementing route optimization software, businesses can reduce fuel consumption and transportation costs.
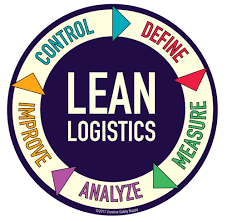
Improved Quality:
Lean logistics practices can also improve the quality of goods and services. By eliminating waste and streamlining processes, businesses can reduce the likelihood of errors and defects. This leads to improved customer satisfaction and a stronger reputation for quality. For example, by implementing quality control measures, businesses can reduce the likelihood of product recalls and returns.
Improved Flexibility:
Lean logistics practices can also improve the flexibility of businesses. By eliminating waste and streamlining processes, businesses can respond more quickly to changing customer demands and market conditions. This leads to improved agility and a stronger competitive position. For example, by implementing a pull system, businesses can respond quickly to changes in demand without overproducing and creating excess inventory.
Improved Collaboration:
Lean logistics practices also encourage collaboration and communication within businesses. By involving all stakeholders in the process, businesses can improve coordination and reduce the likelihood of errors. This leads to improved teamwork and a stronger organizational culture. For example, by implementing cross-functional teams, businesses can improve communication and collaboration between different departments.
Better Inventory Management:
Lean logistics practices can help businesses optimize their inventory levels by reducing excess inventory and improving inventory accuracy. This can help businesses reduce carrying costs and improve cash flow.
Continuous Improvement:
Lean logistics practices are based on the principle of continuous improvement. By continually reviewing and optimizing processes, businesses can achieve ongoing improvements in efficiency, quality, and customer satisfaction.
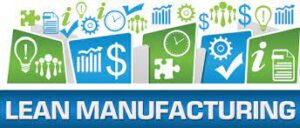
Implementing Lean Logistics Practices:
To successfully implement lean logistics practices, businesses must take several steps. First, it is essential to identify and eliminate waste throughout the supply chain. This can include excess inventory, unnecessary movement of goods, and overproduction. Businesses can use tools such as value stream mapping and Kaizen events to identify waste and implement changes to eliminate it.
Another critical step is to optimize processes for efficiency. This can include improving communication and collaboration between suppliers, carriers, and customers, implementing just-in-time delivery practices, and using technology to automate processes.
To ensure quality, businesses should implement quality control processes and measure performance metrics regularly. This can include monitoring on-time delivery rates, defect rates, and customer satisfaction scores.
Enhancing flexibility requires businesses to be proactive in identifying potential disruptions and developing contingency plans. This can include building relationships with alternative suppliers and carriers, maintaining safety stock of critical products, and implementing flexible production and shipping schedules.
To implement lean logistics practices, businesses need to adopt a systematic approach. This can involve a range of activities, including:
- Mapping current processes to identify areas of waste and inefficiency.
- Developing a plan to eliminate waste and optimize processes.
- Implementing changes and monitoring results.
- Continuously reviewing and improving processes.
Case Study: Toyota’s Lean Logistics Practices
One well-known example of successful lean logistics practices is Toyota’s supply chain management system. Toyota has implemented lean principles throughout its supply chain, from manufacturing to delivery. By focusing on waste reduction, process optimization, and quality control, Toyota has achieved exceptional efficiency and cost savings.
One example of Toyota’s lean logistics practices is its just-in-time delivery system. Suppliers deliver parts and components to Toyota’s manufacturing facilities precisely when they are needed, eliminating the need for excess inventory and reducing the risk of overproduction.
Examples of Successful Implementation of Lean Logistics Practices:
Many businesses have successfully implemented lean logistics practices and have achieved significant benefits. For example, the multinational consumer goods company, Procter & Gamble, has implemented a lean logistics strategy that has resulted in significant cost savings and improved efficiency.
Here are some additional points to consider regarding the benefits of lean logistics practices for businesses:
Improved Safety: Lean logistics practices can also lead to improved safety in the workplace. By reducing waste and optimizing processes, businesses can eliminate hazards and reduce the risk of accidents.
Increased Capacity: Lean logistics practices can also help businesses increase their capacity without increasing costs. By improving efficiency and reducing waste, businesses can increase their output without investing in additional resources.
Better Communication: Lean logistics practices can also improve communication between different departments in a business. By streamlining processes and eliminating waste, businesses can create a more cohesive and collaborative work environment, which can improve communication and reduce misunderstandings.
Improved Employee Morale: Lean logistics practices can also have a positive impact on employee morale. By eliminating waste and improving processes, businesses can reduce frustration and stress among employees, which can lead to a more engaged and motivated workforce.
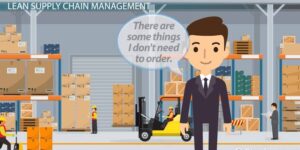
Better Data Management: Finally, lean logistics practices can also help businesses improve their data management capabilities. By optimizing processes and reducing waste, businesses can collect and analyze data more effectively, which can help them make better decisions and improve their overall performance.
Conclusion
The benefits of lean logistics practices are numerous and can have a significant impact on a business’s operations and bottom line. By adopting a systematic approach to process improvement and waste reduction, businesses can achieve greater efficiency, cost savings, and customer satisfaction, while also improving safety, communication, employee morale, and data management capabilities.